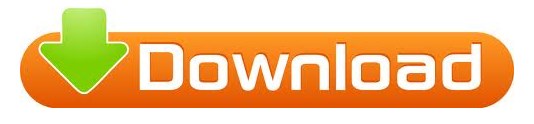
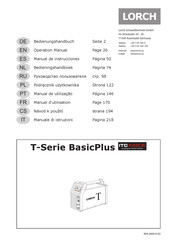
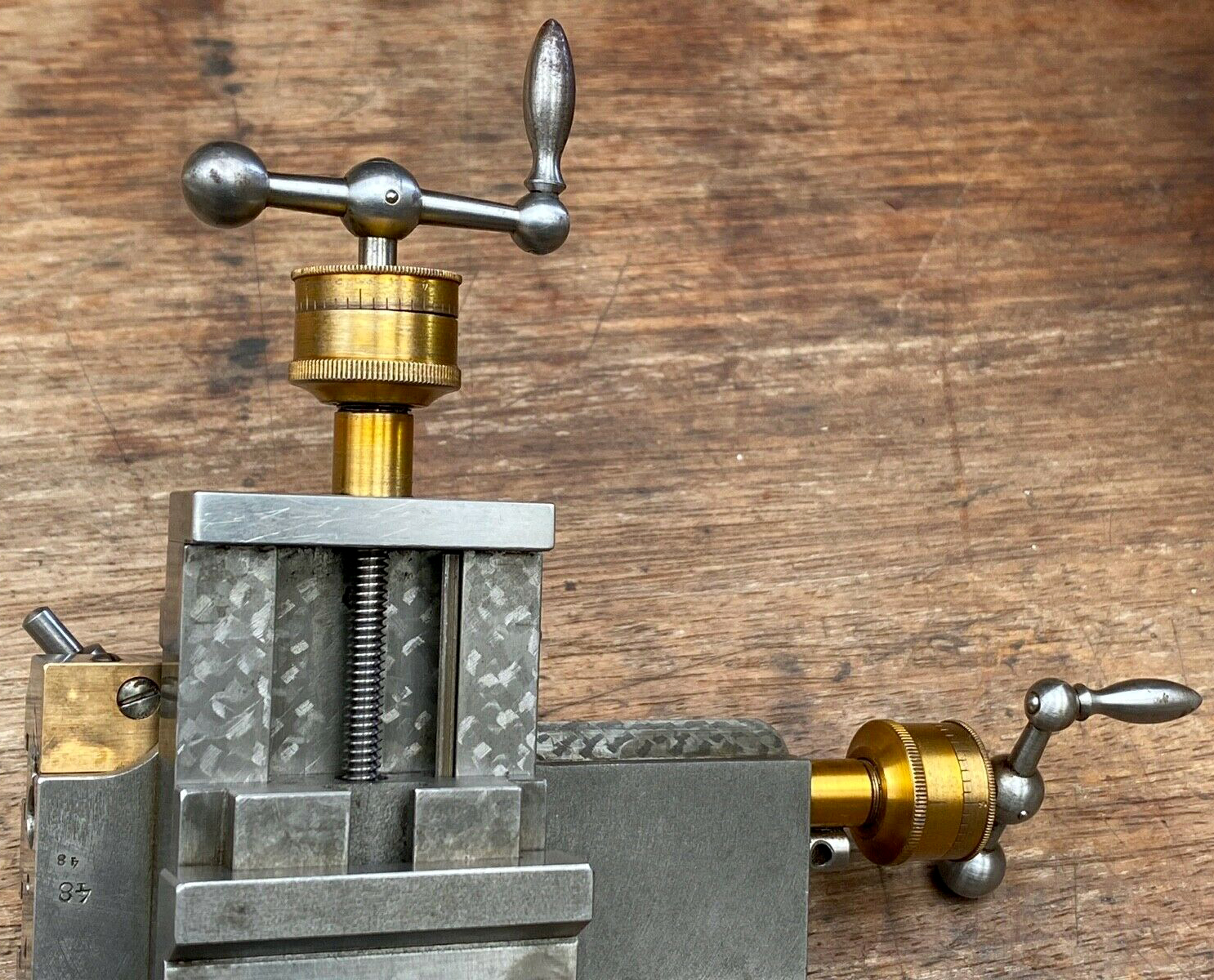
Welding and cutting machines must be used appro- priate and only by specialist staff. : Safety Precautions Safety precautions Requirement Use and maintenance of welding and cutting machines can be dangerous. Early-model Lorch AV1-L with a screwcutting gearbox and a separate shaft to drive the sliding and surfacing feeds.Page of 27 Go.
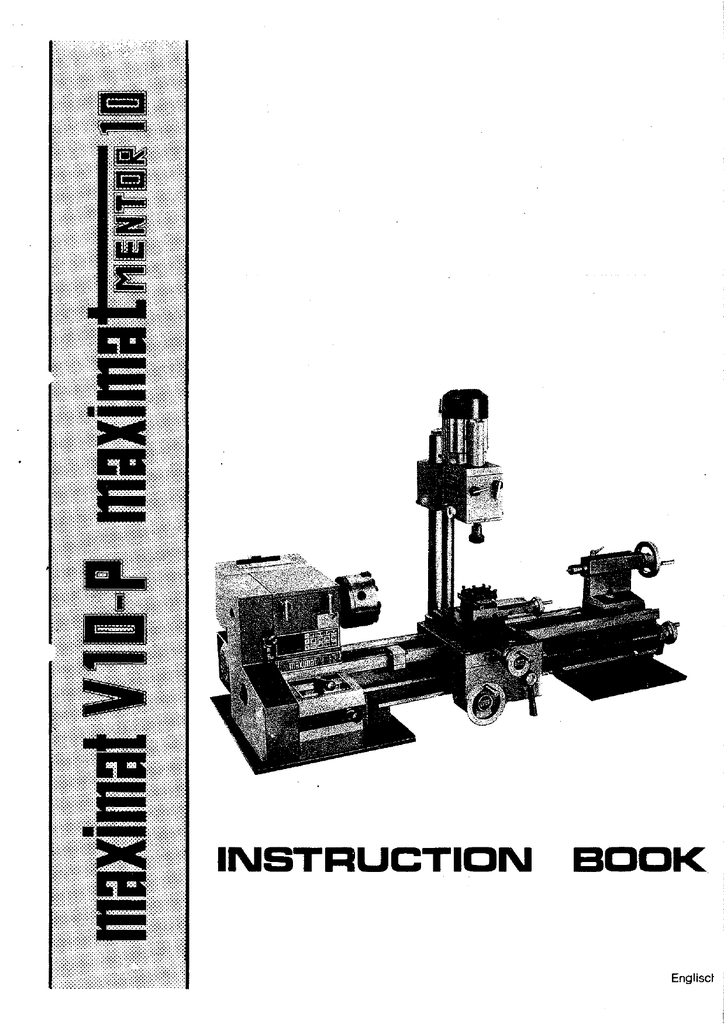

Screwcutting by changewheels and no power cross feed. If you have a Lorch lathe that resembles the ones shown on this page the writer would be very interested to hear from you. Because the lathe was so very expensive and of a rather ordinary specification - though the build quality was of the highest order and the accuracy unquestioned - it must have sold in comparatively low numbers and today is rare. Screwcutting on the later model was by a large diameter, 8 t. A single lever both engaged and disengaged the helical backgear assembly, there being no pins to pull out and push in or other unnecessary fumblings. Just one bed length was offered - admitting around Spindle speeds spanned 48 to rpm with the single-speed motor - and 48 to rpm with the two-speed. One most useful fitting was an adjustable knock-off stop on the power sliding feed that allowed slow jobs on the finest feed to be left working in the knowledge that, when finished, the drive would be safely disengaged. The later model was somewhat cheapened and offered screwcutting by changewheels only there appears to have been no option of a screwcutting gearboxlost its separate power shaft and power cross-feed facility and had its handy single-lever backgear engagement mechanism altered. Not a challenge at all if you have the Lorch MX To the MX Also completely automated if required.Although little is known about the chronology of the model, it appears to have been built in early and heavily-modified late versions-the first retaining the traditional Lorch micrometer dials and having the option of power sliding and surfacing feeds from a separate power-shaft and a screwcutting and feeds gearbox - though the latter produced only a very limited number of threads and feeds. Hard installation work, inspections looming, all trades are rushing to finish the job.Ĭostly rework or delays are out of the question. You simply control everything else using the material thickness - ingenious in this class. The automatic setting control of the M-Pro handles the rest. An inclined torch connection for optimum wire guidance aand furthermore pure synergy. Lorch MicorMIG sets new standards and makes switching to a modern, infinitely variable welding system as easy and effective as can be.Īlso, certified in accordance with EN To the most powerful MicorMIG. Whether you are working with steel, stainless steel or aluminium - the pulse process is guaranteed to produce low-spatter welding results along the entire characteristic curve without any laborious rework. The MicorMIG eliminates tedious rework and saves you valuable time while changing the welding wire. It is ideal for narrow joints, saves material and achieves higher strength due to the improved deeper penetration. We offer an incredibly stable and easy to control arc across the complete current range.
#Lorch lathe instruction manual series#
The P series is already impressive with outstanding MIG-MAG welding characteristics which let every welder work more easily and in a more productive way. This is what we call welding at the pulse of time. Add the extremely robust and stable properties of the arc, and you will get: improved handling, higher quality with next to no spatter and, consequently, a much lower amount of rework. This is assured by the patented control technology of the new Lorch S-series.
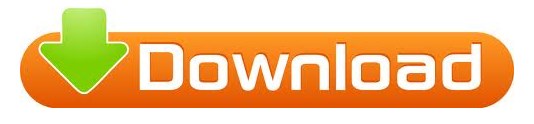